Mid Kansas Coop (MKC) performs first facility train shuttle loadout, approximately 4 minutes from bin to train, including controlling the blend of the grain as it was blended into the shipping leg.
MKC (Mid Kansas Coop) performed extensive market analysis to determine the perfect location for their facility located three miles west of Canton, Kansas. First and foremost, the facility addresses the farmers’ needs to unload grain efficiently and quickly while utilizing technology and equipment to handle high speed loadout to shuttle trains. From physical design of the pits to monitoring many aspects of the system, safety has been a priority in the development of the facility. The system is capable of loading out 110 rail car shuttles at a rate of 100,000 bushels per hour with an annual loadout expectation of 17 to 20 million bushels per year. The layout of the facility allows for both trains and trucks to keep constantly moving with one of the only privately owned bridges over the railroad tracks on the Union Pacific Railroad.
The Canton facility is a cement slip form elevator capable of holding 1.15 million bushels. It can receive up to 60,000 bushels per hour with three legs running at 20,000 bushels per hour. The facility provides farmers with a double-scale system where inbound and outbound trucks can be weighed. The scales are automated with RFID and a person is available for changes if needed. There are two 1,200 bushel pits for semis and large trucks, and a third 600 bushel pit for smaller loads. All pits can feed any bin in the facility or load directly to rail cars.
The system is highly automated with the help of Kasa Controls & Automation and the use of their database programming team. With many different pieces of equipment and systems to manage, Kasa provides overview screens, monitoring screens, alarms and reports into one location for simpler diagnostics and review of the system. Many times, the status of a remote piece of equipment like a bucket elevator can be reviewed at the control center. The fewer times an employee has to physically go out to monitor the equipment results in a safer environment for employees.
Not only do the controls and software enhance the safety aspect of running a grain elevator, quality of the grain is improved with the use of monitors that check the outside temperature and humidity along with the grain temperature and humidity in the grain bins to control the moisture and temperature of the grain with aeration fans. The system uses a formula resulting in an equilibrium of moisture content so the quality of the grain remains high. The system warns and notifies employees of hot spots in order to provide better quality.
Shuttle Train Loadout Project
Upon completion of the grain elevator, one of the final major tests was the shuttle loadout. On a very cold and early December morning, the first shuttle was ready to be loaded.
Engineers from Kasa were on-site to witness the successful transfer of grain from bins to 109 hopper cars. Typically, 110 cars are loaded at a time to deliver to facilities in the Gulf Coast, Pacific Northwest and elsewhere. The Canton Grain Terminal includes a loop track that has room for up to 120 hopper cars.
From Bins to Train
The day began with a 15-minute safety meeting at 6 a.m. that included seven MKC employees and three employees from the Kansas Grain Inspection Service (KGIS). The plans for the day were reviewed and the group dispersed to complete the first task.
The task: bottom hoppers of all 109 cars in the shuttle had to be sealed to guarantee the quality of the product and avoid losses while enroute to the final destination. In this instance, numbered zip tie style seals were used to secure each hopper from tampering. Each car in the shuttle had three hoppers to be tied off. This process was completed in just under an hour by two MKC employees.
The train was then moved into position for loading. Loading of the first car began at 8:15 a.m. and completed at 8:19 a.m. The car contained roughly 4,000 bushels of grain. Four minutes from bins to a hopper car. It took roughly 35-40 seconds to move the next car into position. Shortly after 4:00 p.m., all 109 cars were completely loaded.
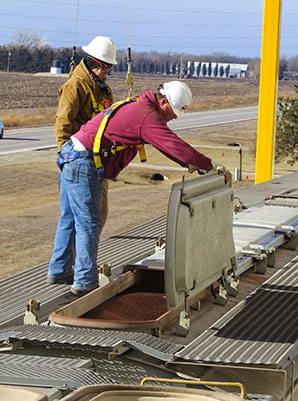
What’s Really Going On
Although it sounds pretty simple, there are multiple tasks being completed behind the scenes to ensure the end customer receives exactly what they are expecting from MKC.
Once it is determined what the customer wants, the facility confirms the commodity is in stock. The commodity then has to be blended out of the facility to the exact specifications of the customer. For this first shuttle loadout, there were seventeen different bins of sorghum to choose from to meet the customer’s needs. The grain was blended and conveyed at over 60,000 bushels per hour into the rail cars. Even a small misjudgment in the blending process could have created a big mess in a short amount of time. Blending software created by Konnection helps make decisions behind the scenes and prevents this from happening. One minute at the wrong blend amounts to over 1,000 bushels of grain (think of slightly more than a full semi-truckload) that would not meet the customer’s specification.
During this first shuttle loadout, one employee operator was dedicated to controlling the blend of the grain as it was pulled from the bins and blended into the shipping leg. He was able to move throughout the facility, the main office, the truck unload control area/KGIS grading room and the rail loadout control room throughout the shuttle loading.
There were four additional Canton terminal employees with specific jobs.
The train driver had the complicated task of moving the train cars into position under the loadout spout to receive the blended grain. The driver also had the critically important job of listening closely to commands from the loadout controller and the rest of the crew. The biggest time issues related to his task came from managing the knuckle-slack. Every time the train is moved, the hopper car connectors (knuckles) tighten when the train moves forward and loosen when it stops. As the cars are filled, the weight of the load is changing continuously which increases the difficulty of properly positioning the hopper cars. This part of the process needs the most adjustment. Kasa engineers believe that the terminal operators will be able to get this part of the process smoother and achieve a 3 minute 30 second loadout per car very soon.
The loadout controller (who also runs the scale), operated the console that controls the conveyor and loadout spout. This is where the grain is transferred from the shipping leg to a covered conveyor and into the car through the loadout spout.
There are also employees who are referred to as train runners. Their task was to open and close the lids on the cars as they were being filled and completed. Once each car was filled, the lid was closed and sealed. The next car was then moved into position under the loading spout.
Once the team finished loading, the train was parked until the railroad picked it up and delivered the hopper cars to their final destination.
To learn more about how Kasa might be able to elevate your grain operations, contact us today.