Variable frequency drives, or VFDs, provide efficient use of power, allow for productivity and control under different types of torque loads, and more.
After some brief information regarding motor controllers and torque loads, let’s explore the ABCs of these beneficial solutions – the applications, benefits and cost savings.
Different Types of Motor Controllers and Torque Loads
The core types of motor controllers are across the line motor starters, which come in full voltage non-reversing and full voltage reversing, soft start/stop controllers, and VFDs.

Across the line, full voltage starters send full voltage, typically 480VAC, to the motor – usually with an accompanying “clunk” that can even dim the lights. Essentially, these motor starters go “full throttle” as soon as they’re turned on.
That issue is slightly alleviated by soft start/stop motor controllers, which use a solid-state electronic device to ramp up the speed of the motor from 0 to 100% over a predetermined amount of time. It works the same way as it stops. This results in less wear and tear on the motor, but these still always go to full speed.
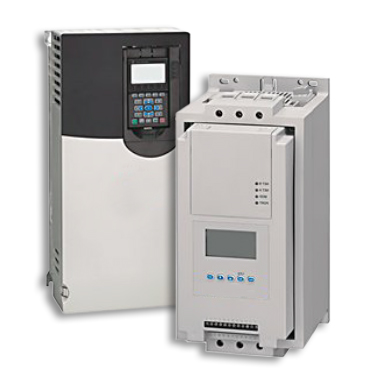
Finally, there are VFDs. Mountable in a motor control center or standalone, VFDs allow for the adjustment of motor speed over time, providing finer control while still realizing the benefits of less wear and tear on the motor.
There are also two central types of torque load. Constant torque loads exhibit roughly the same requirements, regardless of operating speed, while variable torque loads exhibit torque requirements that rapidly increase alongside machine speed.
In constant torque load applications, energy use is roughly proportional to speed. In variable torque load applications, energy savings aren’t linear.
Applications, Such as Grain Handling, Benefits, and Cost Savings
In comparing soft start/stop controllers to VFDs, SS controllers are primarily used for energy savings and to prevent excess wear and tear on equipment.
However, in applications such as grain handling, VFDs provide those same benefits while also offering the ability to adjust speed as necessary.
Let’s look at some scenarios to get a clearer picture.
Scenario #1: Run leg at a lower speed when no grain is present, then elevate to full speed when grain is in the pit prior to the leg.

Since a bucket elevator or leg is a constant torque application, the energy savings are linear. If you slow down to 80% of full speed, you’re saving 20% of energy spent, and so on. But, to move grain, you have to run the leg at full speed.
Scenario #2: Run leg at a lower speed all day, with or without grain, when slow on trucks.
Again, since legs are a constant load application, a slower speed would mean lower energy use. VFDs also allow you to adjust the leg speed for different commodities to help you consider all variables and ensure proper discharge.
There are many other uses cases in which a VFD can provide measurable benefits to your operation, such as their use on screw or auger conveyors for speed and rate of flow adjustments and on pit drags.
Though installation costs are higher and there are other special considerations, such as more training for techs performing maintenance and special considerations to take into account, the added flexibility and easing of wear and tear on motors can alleviate those costs over the life of the controller, providing significant ROI.
Kasa Controls & Automation is here to help you determine if a VFD might be the best fit for your unique needs and application. To learn more, contact us today.