
Aerospace - Chart Recorder Replacement
A large aerospace customer's analog chart recorders were replaced with the latest in technology.
The upgrades Kasa Controls and Automation added on this project added value to our customer in the following ways:
- eliminating paper records - saving labor and time
- reducing liability - helping our customer meet quality standards
- eliminating the manual tracking of data - saving labor and time
- improving the quality of their anodized parts
- paper data-tracking and storage - saving storage space, labor and time
Anodizing Data Tracking & Storage
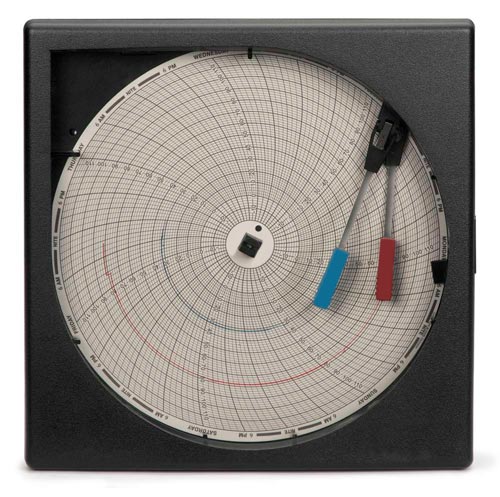
A circular chart recorder (data logger) records an electrical or mechanical input trend onto a piece of paper, resembling a record player. Each very thin paper disc has to be changed often and stored for decades (to potentially be retrieved from a storage warehouse) in the event that the data is ever required for review, or a quality issue occurs and is investigated. (Imagine the time involved trying to manage, store and retrieve one thin paper disc in a warehouse that has collected 30+ years of this data.)
Demand for this upgrade was driven by top management to plant engineers who contacted Kasa for help in addressing the following issues:
- meeting quality standards
- data tracking/storage
- process elimination
Before the upgrade of this system, a temperature gauge was mounted to the side of each tank and was connected to a temperature sensor inside the tank, There was no alarming or notification if a tank's temperature went outside of its threshold. The operator had to constantly walk to each tank and monitor the temperature, as well as, periodically record it on a piece of paper.
Kasa upgraded this process by installing thermocouple temperature sensors in each tank and wiring each one back to a Programmable Logic Controller (PLC). Additionally, an HMI was connected to the PLC so the operators would have a visual of the system.
The system is now capable of graphically representing the following:
- real-time tak temperatures
- historical trends of tank temperatures
- visual and audible alarms if tank temperature is outside of threshold
- email notifications to line supervisors if tank temperature is outside of threshold
- record the temperature value of a tank and store it to the database every 4 minutes
In addition to the tank temperatures, the rectifiers used for anodizing also required data collection. Any time parts are submerged in either of the anodizing tanks, the rectifier voltage and current must be recorded every ONE second in order to ensure quality.
The data provided is critical for this customer. If they miss ONE second of data tracking while processing the part, the part has to be reworked (parts are used on airplanes and MUST pass quality testing by their customer or they will lose contracts and customers).
Tying Controls into PLC
Before tying controls into the PLCs, tanks had rudimentary self-actuating valves with springs to compress/decompress to open and close valves to regulate steam temperatures. There was zero uniformity with the valves being used.
Kasa installed Proportional Integral Derivative (PID) loops (feedback system). This system tells the tank what set point it needs to maintain (i.e. 86°). The calculations are based on data transferred (this works similarly to cruise control on cars) and causes the valve to open/close based on input/output to both maintain and control temperatures.
Kasa also standardized tank valves, thus reducing spare parts inventory.
Installing Anodizing Rectifiers
Anodizing rectifiers were installed, replacing 20+ year old equipment prone to failure.
Anodizing rectifiers are very similar to controls cabinets. Rectifiers (power supply) are electrical devices that supply current for the anodizing process. 480VAC power is converted into a DC signal to regulate the current throughout the anodizing process. Kasa supervised the electrical installation of the new rectifiers minimizing production downtime.